Construction 4.0
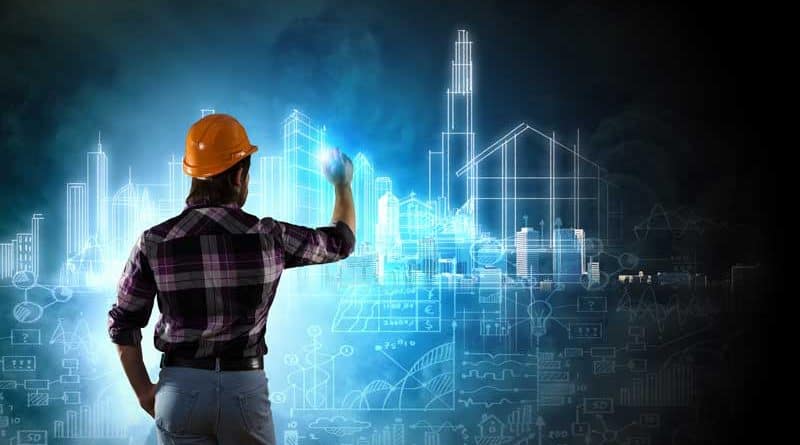
What is Construction 4.0?
Construction 4.0 is the construction industry’s version of Industry 4.0. In other words, the term represents the digitization of the construction industry. Technologies like robotics, 3D printing, machine learning, and AI are gradually being introduced to the sector, which while exciting, represents changes that teams will need to understand.
Construction companies still rely on manual labor, heavy machinery, and a business model that hasn’t seen much change in the past 50+ years.
Below is an illustration of 10 disruptive technologies in construction, as predicted by the World Economic Forum. The graphic shows the massive impact construction 4.0 will have on the industry as change is coming from all directions.
Procurement teams will need to consider pre-fabrication and 3D printing along with traditional sourcing methods. Virtual and augmented reality and connected equipment will enter the mix. And, like every other industry, big data will become mandatory.
Investment in construction technology has doubled over the past decade. According to McKinsey, the lion’s share of spending is going toward back-office technology like SaaS products or cloud computing, as well as building and modeling software. Other areas like artificial intelligence and 3D printing are expected to see more adoption down the road.
Technologies
While the basis of Industry 4.0 in many industries relies on the technologies which enable ubiquitous connectivity and real-time decentralized decision-making, Construction 4.0 is not limited to those technologies but rather based on a broader spectrum, with the main ones being the Internet of Things, Digital Twin, additive manufacturing, cloud computing, Cyber-Physical Systems (CPS) and, of course, BIM.
The great promise of the Construction 4.0 revolution lies in the almost complete automation of the entire project life cycle. This automation involves the use of digital twins at every step, from planning to operation, including design and construction. In the design phase, the increased use of BIM models as digital twins makes it possible to question them through simulations of the physical product (the building, for example), its constructability and profitability options (4D, 5D), and its sustainability (e.g., energy analysis).
In the construction phase, BIM models continue to serve as digital twins, but are complemented by other technologies to automate their connection to the reality of the construction site. These technologies are mainly Cyber-Physical Production Systems (CPPS), including sensors, drones, embedded robotics and monitoring systems. In the operational phase, the BIM and the IoT, together with other CPS sensors, make it possible to monitor the performance of the facility and to set up an effective system for preventive maintenance management.
4.0 Technologies in Construction Industry
Supply Chain Optimization
According to that same McKinsey report, procurement and supply chain management are still relatively cumbersome, mostly manual processes.
Some startups have seen that procurement processes need to change with the times, and increasingly, there’s a move toward creating online marketplaces for buying and selling raw materials, equipment, and even finding new subcontractors.
The benefit, as stated in the report is that players can match supply to demand and even enhance competitive bidding.
Another area that’s gaining more traction is prefabrication. Construction, as it’s been for thousands of years is a repetitive process. If teams can purchase partially constructed components in advance, they could complete projects in less time.
3D Printing and Procurement
Additive manufacturing or 3D printing has been around for a while now, but it’s beginning to shake up construction logistics — impacting everything from production, sourcing, and planning to how procurement approaches vendor relationships.
3D printing does present a few key challenges—beyond purchasing the equipment, of course.
One is understanding which items are best suited for 3D printing. Teams must understand which items they can’t print and which parts are cheaper to buy outright. Additionally, they will need to apply strategic methods to sourcing raw materials required for printing new parts.
The other big challenge lies in IP and licensing. Procurement pros may need to shift their focus on negotiating IP deals with vendors who own the rights to print a specific part.
Lean Construction
The idea of lean construction is centered around maximizing value for the customer while minimizing waste. It’s not exactly a new idea. In fact, Toyota developed the approach following World War II when supplies were scarce. However, it’s much easier to develop a lean approach to manufacturing when the bulk of the work takes place within the walls of a single factory—allowing for predictable forecasting and control over processes.
In construction, the aim of going lean is to focus on sustainability and efficiency. So, the process depends on project planning methods that achieve a continuous workflow, while minimizing downtime, overproduction, and wasted workforce.
What is new is, the use of technology to reduce waste in construction. Tools like cloud-based project management and procurement software play a role in establishing a lean construction strategy, as they provide increased visibility and real-time updates.
BIM
Other technologies like Building Information Modeling (BIM) and augmented or virtual reality can reduce waste, too. One example is, we now have access to 3D designs that allow clients to see how a project will turn out, before building begins. This might reduce instances of late-stage change that leads to waste and overruns.
Speaking of BIM, this technology is also gaining significant traction in the construction business. BIM creates 3D visual representations of construction projects.
While construction companies have long used 3D models, the latest BIM technology facilitates a more collaborative planning process. All stakeholders from manager to designer to client and subcontractor can add their input to a project. Later, teams can use this information to decrease building waste and get everyone on the same page.
Automation in the Back-Office
One issue we’ve seen come up over and over is this idea that the hardest part of adopting new technologies is the people, which makes sense. PwC’s Industry 4.0 report stated that all employees must “think like digital natives.”
According to another McKinsey piece, construction companies will need to improve their training process across the following areas: Project Planning, Performance Management, Risk Management, Sourcing Strategy.
Big Data and Decision-Making Platform
The volume, the variety, and the need of velocity of these data will require the use of platforms adapted to interpret them, manage them, but also and especially to connect them to the existing business platforms.
The systems required will therefore not be just Big Bata or decision-making platforms, but rather matchmaking platforms, providing new innovative services and products that connect the construction site with smart factories, and with more smart design and use of connected smart buildings (or cities).