Food & Beverage 4.0
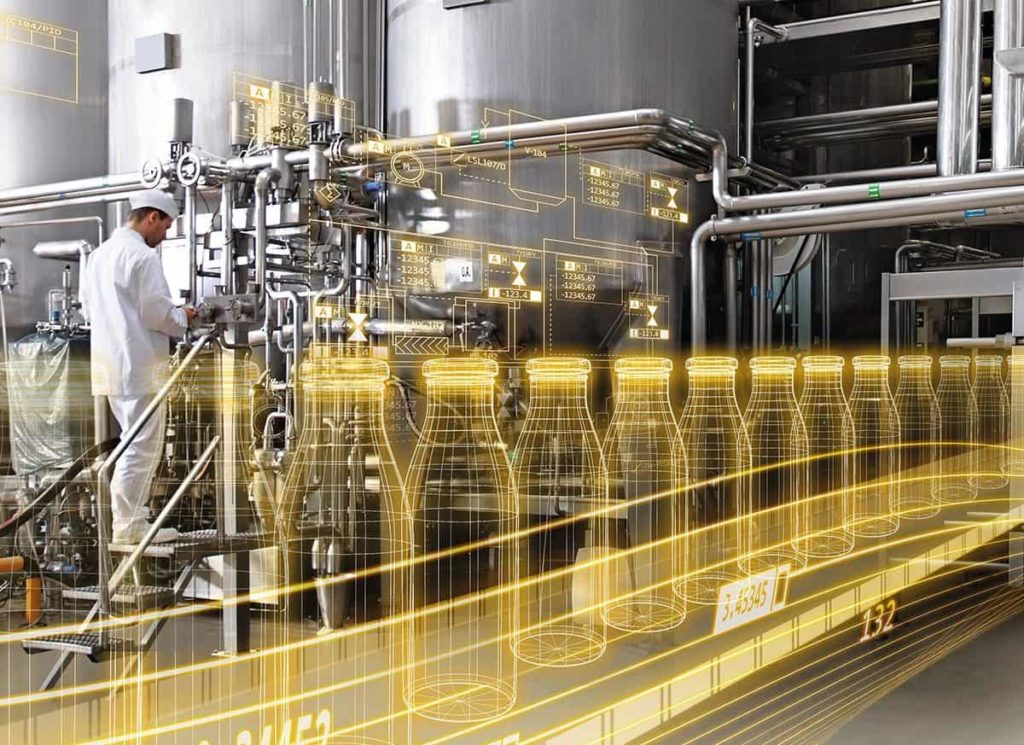
The food and beverage industry is more competitive than ever. A global market and consumers’ ever-changing tastes leave no room for error, so plants need to be able to act quickly and adjust to maintain profit margins. Facilities that embrace the Industrial Internet of Things, or IIoT, will remain competitive while those that don’t will be left behind.
In order to fully embrace Industry 4.0, facilities have a number of needs that must be met. They’ll need more types of reliable and accurate data, a system to analyze the data, and finally, a way to act on that analysis. At first glance, each of these needs may appear to be big obstacles to overcome, but upon further inspection, these are simply opportunities for continuous improvement.
Acquiring all of this data is a big endeavor, but it’s made easier with new and advanced sensor technologies. Smart pressure sensors, point level switches, and radar level sensors already help plants automate processes, improve efficiency, and save energy. Bringing all the sensor process data together using the IIoT will help drive smarter and faster complex business decisions, which will only help to make further improvements to efficiency and energy conservation.
What is Food & Beverage 4.0?
The face of the Food industry is changing. With the Internet of Things (IoT) technologies, cloud computing, cognitive computing and virtual reality helping bridge the gap between the cyber and physical realms, there is greater innovation and automation in the Food & Beverage industry.
Industry 4.0 is the new trend that’s pervading industries across the world. Greater automation is creating smarter factories with even smarter operations. Cyber systems are being introduced to control physical processes. Control and traceability are largely possible due to virtual blueprints of operations available on centralized networks.
In the Food industry, Industry 4.0 is changing the way raw materials are procured, food is manufactured, packets are packaged and items are sold. Essentially, the entire journey from farm to table is being analyzed, controlled and is continuously evolving through virtual systems.
Technologies
Cyber-physical systems communicate with the machinery and software put into place by manufacturers, suppliers and retailers. This allows greater collaboration across divisions and even organizations. Additionally, these systems offer organizations multiple benefits such as:
- Automated tracking of materials and packaged products through utilization of Radio Frequency Identification (RFID) tags and ERP systems
- Quality maintenance of products through horizontal integration of processes across divisions and organizations
- Waste management and carbon footprint reduction through resource management software
- Increased production rate and reduced downtime due to interoperability of systems
- Greater transparency in data sharing through collaborative platforms
4.0 Technologies in Food & Beverage Industry
Food Production in the Digital Space
Industry 4.0 works based on four tenets:
- Decentralization of decision-making
- Interoperability
- Technical support
- Information and process transparency
Moving food manufacturing into the digital space allows organizations to control their processes up to the minutest degree. The ability to chart each step in advance and control the output allows organizations to tackle macro-level world issues such as global hunger, changing food safety requirements and evolving customer tastes.
Product information sharing
Product information sharing has always been an integral task for organizations in the Food & Beverage industry.
Global compliance requirements require manufacturers to share key product information with other parties. With the integration and overlap of cyber-physical systems, Industry 4.0 will allow manufacturers to share their product data with ease.
In fact, a hallmark of Industry 4.0 is collaboration and shareability. Every piece of the data, from raw material specifications to compliance-related product information, will be available on virtual platforms which will be accessible by every stakeholder.
Data Management
Management of business analytics and implementation of business insights will be on the forefront of the Industry 4.0. The integration of cyber-physical systems enables greater access to data. Both current demand requirements and historical supply data can be integrated to understand future projections of demand and supply.
Interconnected systems create multiple touch points which facilitate data sharing. Data analysis and generation of business insights can be easily streamlined, considering the greater accessibility to information. Gamification, AVA-triggered content and edutainment will allow for better information sharing. However, data management in the digital space is not without its fair share of problems.
Personnel development
Industry 4.0 will bring with it the ability to create safer workplaces. The Food & Beverage industry, with its hazardous machinery and complicated manufacturing processes, can be a minefield for untrained and inexperienced workers. Greater integration of systems allows manufacturers to exert safety controls on the factory floor.
One of the best benefits of Industry 4.0 is its large scope –from helping a mechanic identify the machine part to be replaced to assisting the production manager in finding better ways to make workflows more operationally feasible, making this technology extremely beneficial.
Workplace Safety
Technology can help floor supervisors identify danger times and zones and ensure that adequate safety measures are in place. Machinery can be programmed to identify critical limits and can be designed to rectify problems themselves. Tasks which are manual today can be automated tomorrow, further reducing threats to life and limb. This will also help manufacturers reduce production, technology and legal costs.
Additionally, managers can identify key personnel who have the specialized skill set necessary to drive innovation on the factory floor. Employee development is an added advantage, with staff being trained to use the new technology to optimize production, packaging and transportation.
Production-line downtime and the associated costs can be reduced exponentially, as employees are trained to react quickly and safely when new systems fail or break down.
Food Safety
The Food & Beverage industry will see a change in the way ingredients are mixed and used to manufacture products. Synthetic food will come into the limelight, with technology enabling production of safe and edible synthetic materials.
Sustainable production practices can be adopted with the support of technology. The entire farm to table process can be controlled from growing and harvesting the raw materials to processing them. The prevalence of food contaminants will be reduced by setting up preventative procedures. Both quality and quantity of incoming materials can be charted, as well as recalls of soiled products tracked with ease.
Compliance will also become easier as organizations can track their readiness to meet and fulfill compliance requirements. At the end of the day, organizations will find it easier to reflect the values of their customers through sustainable business practices powered by Industry 4.0 technology.